Vibration Detection for Condition Monitoring
Eliminate Unplanned Downtime and Extend Asset Lifespan
Condition-based monitoring (CbM) is defined as a predictive maintenance strategy that continuously monitors the condition of assets using various types of sensors and real-time data extracted from these sensors. Manufacturers utilize the collected data to reduce maintenance costs and asset downtime, ultimately improving throughput and asset utilization. CbM can be used to establish trends, predict failures, calculate asset lifespans, and enhance the safety of manufacturing facilities.
With its deep expertise in detection, signal processing, communication, power management, and system design, combined with leading AI detection and interpretation platforms, ADI (Analog Devices, Inc.) enables its customers to deploy new condition monitoring solutions faster, extracting more value and higher-quality data and insights. ADI's comprehensive system-level solutions provide the technology and insights to create new, high-value predictive maintenance service products for deployed equipment.
Advantages of Condition Monitoring
As manufacturers seek to improve throughput and asset utilization by reducing maintenance costs and asset downtime, real-time continuous condition monitoring and predictive maintenance solutions become increasingly important. Given that the cost of unplanned downtime can account for nearly one-fourth of total manufacturing costs, adopting predictive maintenance solutions has the potential to significantly save costs and boost productivity.
Extend Equipment Lifespan
Real-time monitoring of assets ensures that equipment operates within the manufacturer's specifications, thus extending its lifespan.
Reduce Maintenance Costs
Real-time monitoring of asset health helps schedule maintenance based on the current condition of assets rather than on fixed time intervals, reducing maintenance costs.
Increase Throughput
Condition monitoring improves manufacturing throughput by reducing maintenance downtime and unplanned asset downtime.
Minimize Asset Downtime
Real-time monitoring of asset health helps eliminate unplanned asset downtime.
Accelerating Time-to-Market with CbM Development Platforms
Developing accurate and reliable condition monitoring solutions for industrial assets requires a combination of technical and design considerations, capturing critical signals and transforming them into actionable insights. Our comprehensive technology and platform product offerings include:
Sensor and Signal Chain Design
ADI's high-performance, precision sensing solutions include MEMS inertial, temperature, and magnetic sensors, along with supported signal chains, to provide accurate and reliable data.
Embedded Software Design
Our open-source embedded software carefully samples and processes signals to ensure optimal sensor data for critical decision-making.
Algorithms and Insights
Real-time anomaly and event detection algorithms enhance condition monitoring solutions, allowing deeper insights into overall machine health for actionable insights.
Mechanical System Design
Optimized mechanical mounting of condition monitoring solutions ensures early defect characterization can be extracted from sensor solutions.
Voyager 3 Wireless Vibration Monitoring Platform
Wireless Platform
MEMS-based wireless vibration monitoring kit for accelerated asset monitoring and solution development.
Condition-Based Monitoring (CbM) Development Platform
EVAL-CN0549
Provides high-quality IEPE-compatible sensor data to accelerate condition monitoring algorithm development. Quickly transmit high-quality MEMS vibration sensor data directly into common data analysis tools such as TensorFlow® and MATLAB®.
Integrated Vibration Sensors
ADcmXL3021
Industrial-grade, wideband, low-noise three-axis vibration sensor with built-in signal conditioning for vibration data analysis.
End-to-End System-Level Solutions for Condition Monitoring and Predictive Maintenance
ADI's deep domain knowledge in detection, signal processing, communication, power management, and system design, combined with leading AI detection and interpretation platforms, enables our customers to deploy new condition monitoring solutions faster, extracting more value and higher-quality data and insights. ADI's complete system-level solutions provide the technology and insights to create new, high-value predictive maintenance service products for deployed equipment.
Detection Modules
ADI MEMS accelerometers for vibration and shock detection in CbM applications, leading the industry in low power, low noise, wide bandwidth, and temperature specifications. ADI temperature sensors provide high accuracy and precision through analog and digital outputs.
MEMS Accelerometers
Temperature Sensors
Data Acquisition
High-fidelity data acquisition converts vibration, shock, temperature, acoustic, pressure, voltage, and current signals into digital signals, translating into asset health insights. ADI offers the industry's most comprehensive range of analog-to-digital converters (ADCs) to meet various performance, power, cost, and size requirements.
Precision ADCs
Precision Signal Chain μModule® Solutions
Power Management
ADI's power management products offer small form factor, high-efficiency solutions, enabling compact intelligent sensors to operate in harsh industrial applications. ADI's extensive power management products and design tools help our customers accelerate time-to-market while delivering outstanding performance and reliability.
Power Management
Power Monitoring, Control, and Protection
Edge Processing
ADI's ultra-low-power MCUs enable local decision-making on the node for events occurring in the field, allowing only the most critical data to be sent to the cloud, thus extending battery life for wireless CbM solutions deployed in hard-to-reach locations.
Ultra-Low-Power Microcontrollers
Wired/Wireless Connectivity
ADI's wired and wireless connectivity products are designed for reliability, resilience, and scalability crucial in harsh industrial environments, making them ideal for CbM applications. Utilize our trusted solutions to accelerate CbM deployments, ensuring that critical asset health data is reliably transmitted to PLCs and Manufacturing Execution Systems (MES) for rational maintenance scheduling and the elimination of unplanned downtime.
SmartMesh®
Isolated and Non-Isolated RS-232/RS-422/RS-485
Industrial Ethernet
Edge AI and Cloud Insights
ADI OtoSense™ is an AI-driven platform that can detect and interpret any sound, vibration, pressure, current, or temperature to enable continuous condition monitoring and on-demand diagnostics. ADI OtoSense can self-detect anomalies, learn continuously through interaction with domain experts, and create digital fingerprints to aid in identifying machine failures early, thereby avoiding costly downtime, damage, or major failures.
OtoSense
Key Product Highlights
ADXL1002
Low Noise, High-Frequency ±50g MEMS Accelerometer
AD7768-1
Precision 24-bit ADC with Power Scaling for DC to 204 kHz Dynamic Signal Analysis
LTP5901
SmartMesh IP Wireless 802.15.4e PCBA Module with On-Chip Antenna
More Application-Related Electronic Components

MC79M05CDTRKG
Linear regulators with negative feedback designed to provide a constant 5V output at a maximum current of 500mA

KSZ8895MQXIA
High-speed networking switch
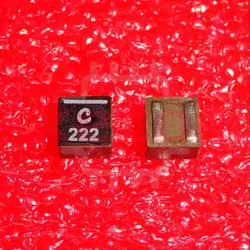
XGL4030-222MEC
2.2uH ±20% 7A 1616 Power Inductors ROHS
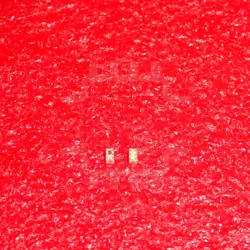
0900LP15B0063E
Ceramic Filters Low Pass 900MHz 0.9dB 50Ohm SMD 8Pin T/R
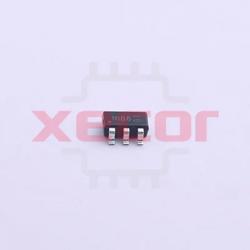
ZXMN10B08E6TA
ZXMN10B08E6TA is a N Channel MOSFET, featuring a voltage rating of 100V and a maximum current of 1.6A, with a low on-resistance of 230mΩ at 10V
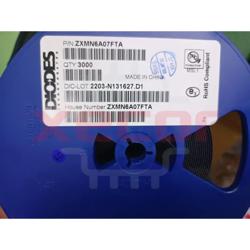
ZXMN6A07FTA
Small Signal Field-Effect Transistor
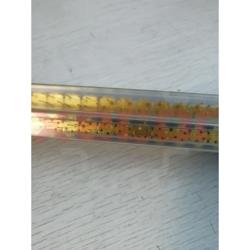
MLX90614ESF-DCI-000-TU
Digital Temperature Sensor MLX90614ESF-DCI-000-TU, Operating Range: -40°C to 85°C, TO39 Enclosure
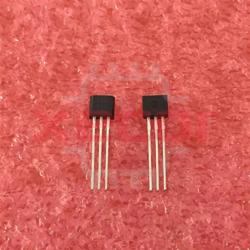
ZVN2106A
channel MOSFET with a voltage rating of 60V, current rating of 0.45A, and power dissipation of 0.7W, packaged in TO92
READ ALSO
-
Industrial Wireless Connectivity Technology Date: 08/10/2023
Wireless communication has been used in industrial applications for many years, initially for basic control of cranes and other mobile equipment. With the adoption of more standardized wireless connectivity technologies in recent decades, control has expanded to a wider range of terminal devices.
-
Industrial Wired Connectivity Technology Date: 08/10/2023
Today, wired connectivity technology remains the primary technology adopted in the industrial sector. Existing factory networks widely utilize legacy serial interfaces to ensure uninterrupted high-performance connections.
-
Vibration Detection for Condition Monitoring Date: 08/10/2023
As manufacturers seek to improve throughput and asset utilization by reducing maintenance costs and asset downtime, real-time continuous condition monitoring and predictive maintenance solutions become increasingly important. Given that the cost of unplanned downtime can account for nearly one-fourth of total manufacturing costs, adopting predictive maintenance solutions has the potential to significantly save costs and boost productivity.