Vehicle Bus Data Recorder Solution
When talking about CAN and LIN bus recording, it usually refers to the recording and analysis of communication data of CAN (Controller Area Network) and LIN (Local Interconnect Network) bus systems. CAN and LIN bus records are important tools for automotive engineers in fault diagnosis, performance analysis and data recording, helping engineers gain an in-depth understanding of the working principle of the vehicle and the interaction between various electronic control systems.
CAN bus record
Typically used for troubleshooting, performance analysis, and data logging. Recording CAN bus communication data can help engineers analyze the operating status of the vehicle and the interaction of various electronic control units. These records can include sensor data, control commands, fault codes and other information related to vehicle functions.
LIN bus recording
The LIN bus is a low-speed serial communication protocol commonly used to connect simple devices in vehicles, such as door control modules, window control modules, etc. Since the LIN bus is often used for interior lighting and auxiliary functions, recording LIN bus communication data can help analyze the interaction process and functional status of these devices.
Recording through specific tools and equipment
CAN and LIN bus logging is generally achieved using specific tools and equipment. These tools can be connected to the vehicle's diagnostic interface (usually an OBD-II interface) or directly to the vehicle's CAN and LIN buses. The recorded data can be saved as a file and then analyzed and interpreted by specific software tools.
Hongke’s data logger solutions
For vehicle bus data recording, the solution proposed by Hongke is to use the CANedge series CAN/LIN bus data recorder. According to different usage occasions and transmission methods (SD card/WiFi/3G/4G), it is easy to use corresponding products Record the bus data in the vehicle to help you complete vehicle telematics processing, OEM research and development, car fault diagnosis and other projects efficiently, conveniently and accurately.
CANedge series CAN/LIN bus data logger
● CANedge1: Collect data through SD card, suitable for pure data recording situations
● CANedge2: Ideal device for collecting data over WiFi, automatically uploading data from your fleet to your server
● CANedge3: Securely collect data over 3G/4G and push it to your server
● Convenient and easy to use: Easily record data of vehicle machinery and equipment and extract data through SD card/WiFi/3G/4G
● Data is interoperable: Collected interoperable data can be processed using your favorite tools/100% free open source software/APIs
● Introduction of GNSS/IMU: The product provides GNSS/IMU data internally, which is recorded together with 2 x CAN/LIN data, supporting higher sensor fusion accuracy, and can add position, attitude, speed, distance, acceleration and other signals
-Ideal for telematics, R&D field testing, diagnostics and predictive maintenance
-Suitable for various GPS antennas
Applications
Application Case 1: Bosch – Recording CAN data for a fleet of electric vehicles
● Bosch needs to use a convenient and safe tool to record the CAN data of the electric vehicle fleet to complete vehicle testing.
● Solution: Install CANedge1 with standalone mode enabled in the test vehicle to record raw CAN data over a longer period of time, and use an SD card to extract the data. Data collection can be completed conveniently and safely without installing a laptop in the vehicle. , helpful for automotive test calibration and optimization of automotive systems.
● Review: “The CANedge1 allowed us to collect data from our test electric fleet and I would definitely recommend it to anyone in need of a CAN data logger.”
Application case 2: Volkswagen of America - safety recording CAN&OBD2 data
● Pain point: Volkswagen of America’s internal testing needs to find a safe, reliable, and fast-running solution to collect OBD2 data and CAN bus data – there are many internal test items that are expensive and time-consuming, and any data can only be controlled by its company servers or backends, meaning that many aftermarket and third-party devices that transfer data to their own backends cannot be used.
● Solution:
Using CANedge2 devices, OBD adapters, and CANCrocodile (convenient link cables) for CAN data collection, data collection can be completed within a week. Customers can also quickly iterate settings to obtain different data points, which is very useful for testing.
CANedge2 creates a sustainable way to conduct passive testing without significant investment from the tester, who simply pulls out the SD card after the test is complete and uses the wifi capabilities provided by the device to transfer the data to the customer's own server and Just execute automated testing.
● Review: “This device costs less and requires less process and time than other internal and external options.”
Application case 3: Diagnostic ECU LIN bus communication
● Pain point: The heater module is not operating as expected and the LIN bus communication between the ECU and the heater module needs to be diagnosed.
● Solution:
The CANedge2 firmware update introduces the LIN recording function. According to the guidance, the firmware update is completed quickly and simply, and LIN data can be automatically recorded without adjusting the configuration.
Used one of the MDF4 converter tools recommended by the support team to convert the *.MF4 log files to CSV, making the records complete and easy to understand, accurately completing the ECU LIN bus communication diagnosis, and smoothly and correctly sending the relevant information from the ECU to in the heater.
Application Case 4: TRL - Recording SoC% from Nissan e-NV200
● Pain point: TRL uses Nissan e-NV200 as a data collection platform and needs to record data on multiple CAN buses to supplement data collected from many other sensors. State of charge (SoC) is the driver (the customer decodes it from EVCAN), but TRL also decodes vehicle speed and wheel speed from CarCAN.
● Solution:
TRL uses CANedge2 and custom OBD-DB9 cables to record both standard CAN and EV CAN. To decode the data, the customer used a Google Sheets workbook from the Nissan Leaf Forum. The e-NV200 CAN bus decoding is very similar to the Nissan Leaf.
For example, the SoC is available on bits 0 to 10 of CAN ID 55B. For a CAN frame with payload b2c0aa00e58013a8, we can take the first 10 bits (1011001011), convert it to decimal (715), and apply a scaling factor of 0.001 to get the charging percentage (71.5%).
● Comments: "This device provided us with a simple and reliable method of data collection. The removable memory card was particularly useful at the end of a day of testing."
Application case 5: Equipment provides GNSS/IMU data, diversified upgrade solutions
● Pain point: Users use the original CANedge series products and want to obtain positioning information on this basis. They need to purchase more products and accessories to assemble and complete the work together. However, the upgraded CANedge series products use the introduction of GNSS/IMU functions, combining them with CANmod.gps into a compact solution.
● Solution:
CANmod.gps is a combined positioning and inertial sensor module that utilizes multiple GNSS signals to achieve optimal positioning, while providing IMU data, supporting sensor fusion models to provide improved positioning information, and transmitting it through the CAN bus.
CANedge has been upgraded to provide GNSS/IMU data internally, which is logged along with 2 x CAN/LIN data. For example, a user who previously needed CANedge2 + CANmod.gps + DB9-Y-shunt + 2 x mounting brackets to complete their data logging now only needs a CANedge2 (including GNSS/IMU) and a GPS antenna to complete their data logging. Data records with optimal positioning information.
● Highlights: The new CANedge series products provide a more compact, scalable, and easier to configure solution, and can also release a CAN channel.
Application Case 6: OEM Prototype Vehicle Fleet Telematics System
● Pain point: Engineers often need to quickly and simply collect real-time data at the prototype vehicle site to complete various testing and R&D work. This work can be easily completed using CANedge3.
● Solution:
First, the user sets up an AWS S3 server (< 5 minutes) and configures the server details onto the device. Then, connect the device to the vehicle to start recording and automatically upload log files via 3G/4G LTE. If desired, customers can also send a request to enable OBD2, UDS or CCP/XCP data logging. In addition, GNSS/IMU data has higher sensor fusion accuracy and can add position, attitude, speed, distance, acceleration and other signals.
CANedge3 can be used in any CAN application including trucks, buses, excavators, cranes and more. The device can log 2 x CAN (like J1939) and request data (like DTC). Data can be uploaded to the server in near real-time for automated processing using Python APIs and more. This allows users to set alerts that provide technicians with instant information on vehicle status, location, and more.
This article introduces you to the technology, product details, and practical application cases of the vehicle bus data recorder solution. Welcome to contact us for more information.
More Application-Related Electronic Components

MC79M05CDTRKG
Linear regulators with negative feedback designed to provide a constant 5V output at a maximum current of 500mA

KSZ8895MQXIA
High-speed networking switch
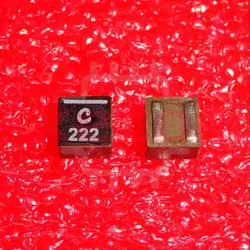
XGL4030-222MEC
2.2uH ±20% 7A 1616 Power Inductors ROHS
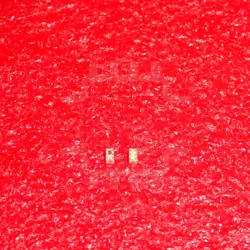
0900LP15B0063E
Ceramic Filters Low Pass 900MHz 0.9dB 50Ohm SMD 8Pin T/R
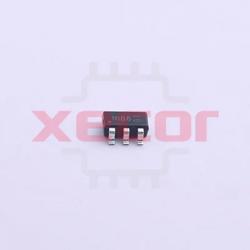
ZXMN10B08E6TA
ZXMN10B08E6TA is a N Channel MOSFET, featuring a voltage rating of 100V and a maximum current of 1.6A, with a low on-resistance of 230mΩ at 10V
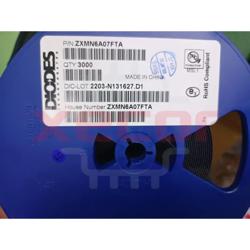
ZXMN6A07FTA
Small Signal Field-Effect Transistor
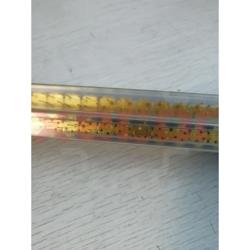
MLX90614ESF-DCI-000-TU
Digital Temperature Sensor MLX90614ESF-DCI-000-TU, Operating Range: -40°C to 85°C, TO39 Enclosure
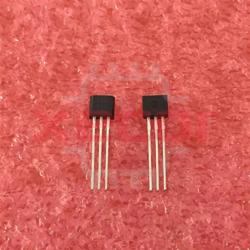
ZVN2106A
channel MOSFET with a voltage rating of 60V, current rating of 0.45A, and power dissipation of 0.7W, packaged in TO92
READ ALSO
-
Automotive OTA Automated Testing Solutions Date: 26/09/2023
OTA technology is one of the symbols of automobile intelligence, and OTA upgrades continue to provide customers with New features continuously enhance user experience.
-
Vehicle Bus Data Recorder Solution Date: 26/09/2023
CAN and LIN bus records are important tools for automotive engineers in fault diagnosis, performance analysis and data recording, helping engineers gain an in-depth understanding of the working principle of the vehicle and the interaction between various electronic control systems.
-
Central computing electronic and electrical architecture solutions Date: 26/09/2023
In the era of intelligent and software-defined cars, whoever can dominate the EE architecture and software can occupy the commanding heights of the smart car market. Therefore, domestic mainstream vehicle companies are also actively making relevant layouts, and mass-produced models with "quasi-centralized" architecture solutions will be launched around 2022-2023.